三葉轉(zhuǎn)子泵的流量是衡量轉(zhuǎn)子泵組性能的重要指標(biāo), 轉(zhuǎn)子泵的內(nèi)泄漏流量對(duì)實(shí)際流量有重大影響,本文以博大泵業(yè)有限公司生產(chǎn)的轉(zhuǎn)子泵組為例,分析影響內(nèi)泄漏的各項(xiàng)因素,針對(duì)轉(zhuǎn)子泵制造時(shí)出現(xiàn)的問題,提出可采取的措施,從理論上計(jì)算并且作出相應(yīng)曲線。
1 內(nèi)泄漏流量計(jì)算公式
1.1 理論計(jì)算公式
三葉轉(zhuǎn)子泵排液腔壓力 Pd遠(yuǎn)大于進(jìn)液腔壓力Ps,排液腔液體
圖1 液體由排液腔向進(jìn)液腔泄漏 通過曲輪與曲輪、曲輪與機(jī)殼以及曲輪與墻板之間的間隙向進(jìn)液腔泄漏 (亞臨界泄漏流動(dòng)) ,稱為轉(zhuǎn)子泵的內(nèi) 泄漏。
內(nèi)泄漏流量為 :
ƒ i──轉(zhuǎn)子間隙通流面積,m2
∆p──升壓值,kPa
ρs──進(jìn)液密度,kg/ m3
計(jì)算前述三種不同泄漏時(shí),αi 取不同數(shù)值。
1.2 曲輪與曲輪、曲輪與機(jī)殼之間的泄漏量計(jì)算
通常按照魏尼希 (Weinig) 和? (Eckert) 計(jì)算亞臨界內(nèi)泄漏流量經(jīng)驗(yàn)公式,曲輪與曲輪、曲輪與機(jī)殼之間的泄漏量為

式中L ──三葉曲輪長(zhǎng)度,m
δ ──間隙值,m
曲輪與曲輪之間的間隙為δbL,曲輪與機(jī)殼之間的間隙為δbr,分別代入式 (2),可以算得曲輪與曲輪之間的泄漏流量 QbL、曲輪與機(jī)殼之間的泄漏流量Qbr 。
1.3 曲輪與前、后墻板之間的泄漏量計(jì)算
曲輪與前、后墻板之間的泄漏量為
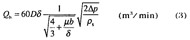
式中D ──三葉曲輪直徑,m
δ──曲輪與前、后墻板之間的間隙,m
μ──系數(shù),μ= 0.02
b ──曲輪端面的平均寬度,m
設(shè)曲輪與前墻板之間的間隙為δb1,曲輪與后墻板之間的間隙為δb2,分別代入式 (3),可以算得曲輪與前墻板之間的泄漏流量 Qb1、曲輪與后墻板之間的泄漏流量 Qb2。
1.4 總內(nèi)泄漏流量的計(jì)算
考慮到上述各處泄漏情況,三葉轉(zhuǎn)子泵工作時(shí)從排液腔向進(jìn)液腔的總泄漏流量
Qbi= 2Qbr+QbL+2Qb1+Qb2 (m3/ min) (4)
2 影響內(nèi)泄漏流量Qbi的因素及解決方式
本文僅分析上述各處間隙值δ、轉(zhuǎn)子泵工作時(shí)的升壓δp 對(duì)Qbi 的影響。由式 (2),影響曲輪與曲輪之間的間隙值 δbL 的因素有:三葉曲輪的設(shè)計(jì)尺寸及公差值、加工安裝精度、轉(zhuǎn)子泵工作時(shí)的溫升引起的熱脹冷縮的影響。間隙 δbL 的控制是轉(zhuǎn)子泵設(shè)計(jì)、裝配要解決的重要問題之一。傳統(tǒng)的工藝方法是將同步齒輪做成整體式,裝配時(shí)控制曲輪與軸、齒輪與軸的位置以及公差值,裝配完成后兩曲輪的追面間隙無法調(diào)整,只能修整葉型曲面。這樣修整后,必定導(dǎo)致間隙δbL增大,使轉(zhuǎn)子泵內(nèi)泄漏流量增大,F(xiàn)介紹一種可以調(diào)整 δbL 的解決方案。
將同步齒輪做成齒輪圈、齒輪轂相配合的型式(如圖 2 所示)。裝配時(shí)先不打用于齒輪圈與齒輪轂之間定位的定位銷孔,轉(zhuǎn)子泵的主從動(dòng)曲輪部、前后墻板與轉(zhuǎn)子泵機(jī)殼裝配后,由于同步齒輪的齒圈與輪轂之間還沒有定位,調(diào)整間隙δbL 使之達(dá)到設(shè)計(jì)要求,擰緊聯(lián)接齒圈與輪轂之間的緊固螺栓,再打定位銷孔,裝入定位銷。這樣,裝配時(shí)有了齒圈與輪轂之間的調(diào)整環(huán)節(jié),裝配出的轉(zhuǎn)子泵的內(nèi)泄漏流量 Qbi 可以較容易地控制在設(shè)計(jì)要求之內(nèi)。
影響曲輪與機(jī)殼之間的間隙值 δbr 的因素有:曲輪的外徑尺寸與機(jī)殼的鏜孔尺寸,以及相應(yīng)的公差值、加工安裝精度等。因?yàn)橹鳌膭?dòng)軸上的固定端軸承安裝在前墻板上,所以曲輪與前墻板之間的間隙δb1 較小;而主、從動(dòng)軸上的游動(dòng)端軸承安裝在后墻板上,曲輪與后墻板之間的間隙δb2 應(yīng)該選取較大的值,以補(bǔ)償轉(zhuǎn)子泵工作時(shí)較高的溫升引起主、從動(dòng)軸的熱脹冷縮的影響。
3 間隙值同內(nèi)泄漏流量Qbi及實(shí)際流量Qs之間的關(guān)系
三葉轉(zhuǎn)子泵工作時(shí)的實(shí)際流量
Qs= Qth-(Qbi+Qbj) (5)
式中 Qth──轉(zhuǎn)子泵的實(shí)際流量,m3/ min
Qbj──轉(zhuǎn)子泵的外泄漏流量,m3/ min
以博大泵業(yè)有限公司生產(chǎn)的 20 m3/ min 流量的轉(zhuǎn)子泵為例,工作轉(zhuǎn)速 n = 450 r/ min,進(jìn)液端壓力 Ps = 101.3 kPa,升壓 ∆P = 490 kPa,進(jìn)液端溫度 Ts = 293 K,排液端溫度 Td = 328 K,工作介質(zhì)為水,曲輪半徑 Rm= 125mm,機(jī)殼鏜孔半徑為125mm,取δ= 0.342 mm,半中心距 a = 88mm,曲輪長(zhǎng)度 L =375 mm,節(jié)圓壓力角 αp = 36.582。
由式 (4) 、式( 5 )計(jì)算后可得 δ- Q關(guān)系見圖 3。
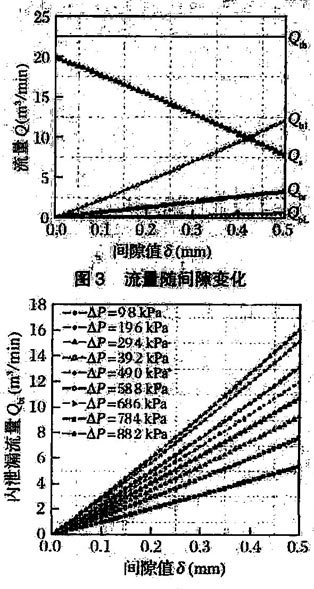
進(jìn)行流量計(jì)算時(shí),認(rèn)為曲輪長(zhǎng)度等于機(jī)殼長(zhǎng)度,所以 QbL 與Qbr 為同一條曲線。曲輪與前、后墻板之間的泄漏量為同一條曲線,間隙 δb1、δb2取不同值,可以得到相應(yīng)的 Qb1與 Qb2。計(jì)算轉(zhuǎn)子泵工作于不同升壓值時(shí)的內(nèi)泄漏情況 δ- Qbi 得到圖 4。
作者用 solidwork 完成圖 1、圖 2,用 mathlab 完成有關(guān)計(jì)算并作出圖 3、圖 4。
4 結(jié)論
(1) 由圖 3 可以看出,曲輪與曲輪之間的間隙δbL、曲輪與機(jī)殼之間的間隙 δbr 對(duì)于三葉轉(zhuǎn)子泵的內(nèi)泄漏流量 Qbi 影響較大,是決定三葉轉(zhuǎn)子泵流量特性的重要影響因素。對(duì)于 20 m3/ min 流量的轉(zhuǎn)子泵,間隙值 δbL、δbr 應(yīng)控制在 0.2 ~ 0.25 mm;安裝固定端軸承的前墻板與曲輪間的間隙 δb1 對(duì)內(nèi)泄漏流量影響較小,可以控制在0.25 ~0.3 mm。
(2) 轉(zhuǎn)子泵工作于不同升壓值 ∆P,其內(nèi)泄漏流量 Qbi隨之發(fā)生變化。在大升壓值 ∆P 的工況下工作的轉(zhuǎn)子泵,應(yīng)采取下列措施:減小轉(zhuǎn)子泵的設(shè)計(jì)間隙值 δbL、δbr,間隙值 δbL、δbr 應(yīng)控制在 0.20 mm 以下;而對(duì)轉(zhuǎn)子泵內(nèi)泄漏影響較小的間隙值 δb1 仍可以控制在 0.25 ~0.3 mm 之間。提高漸開線葉型曲面、三葉曲輪外徑及機(jī)殼鏜孔的加工精度,以保證轉(zhuǎn)子泵的設(shè)計(jì)流量值;而設(shè)計(jì)間隙值 δb1、δb2 范圍適當(dāng)放寬,使加工成本不至于增幅太大。 |